[box type=”info” align=”” class=”” width=””]Mayuri Wijayasundara Lecturer, Deakin University[/box]
- Recycled materials could be used across manufacturing to make production processes greener and more sustainable.
- Significant challenges remain in terms of gaining widespread buy-in from manufacturers to use of recycled materials instead of virgin raw materials, however.
- Investment to scale up recycled material production processes, the use of high-quality data and the development of stable demand for greener products will be key to resolving many of these barriers.
In an ideal circular economy we would not produce waste, but in a linear economy we do. Repurposing this waste to use in new products is one way to recover its value as the world continues along the path to build a circular economy.
A true circular economy promotes more sustainable upstream product design, rather than finding ways to recover and repurpose waste. Careful repurposing of waste-derived material could support this by connecting the upstream and downstream value chains of products. This could lead to iterative improvements in product design that would make it easier to recover components and materials for reuse. Additionally, these products could encourage the development of greener markets and raise awareness of new sustainable choices.
Are recycled materials inferior?
Unfortunately, there are deep-rooted perceptions that waste-derived, recycled or recovered materials are inferior to virgin materials. However, the concept of “quality” in this context mainly depends on use. Since current industrial processes are designed and calibrated to use virgin materials, recycled or recovered materials can disrupt value chains. With some adjustments to their processes, however, it would be possible for manufacturers to gain value from using recovered materials.
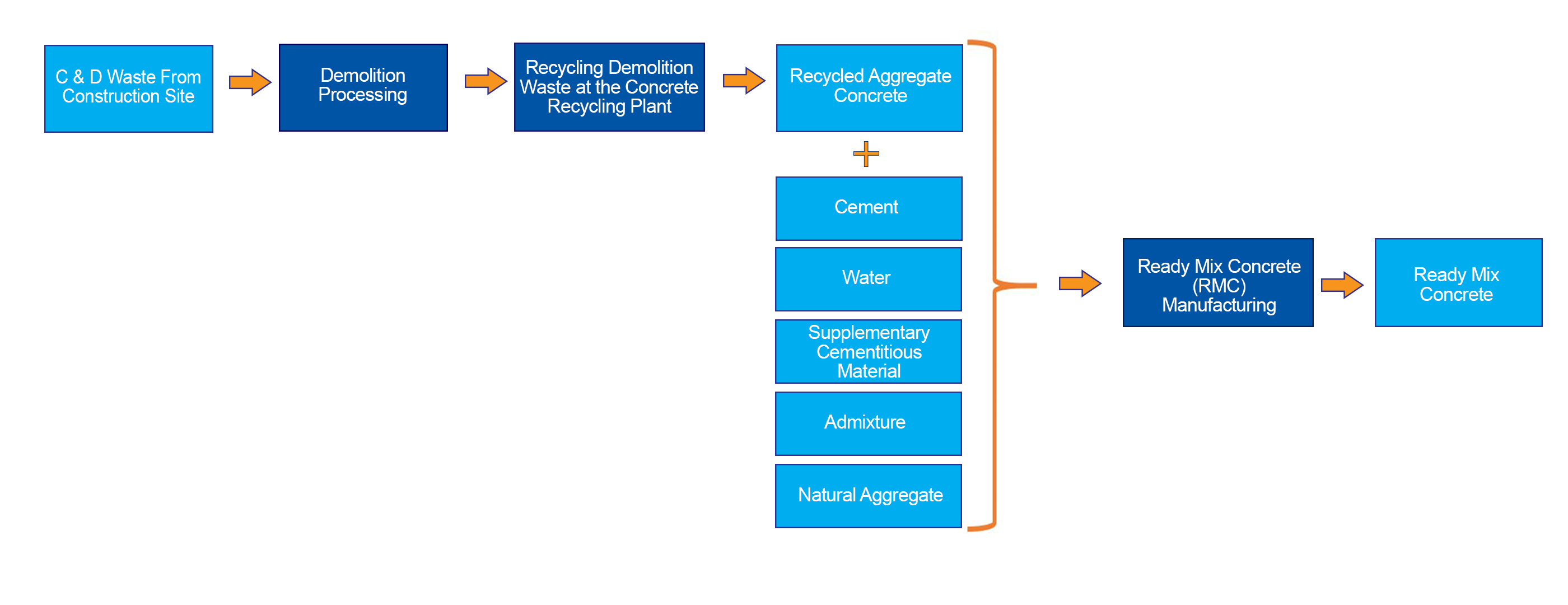
Take, for example, recycled concrete aggregate (RCA). It could replace natural aggregate in the construction industry, but there are 5 major barriers to overcome before it can add real value to the concrete production process:
1) Product contamination and variation
When concrete is produced, waste is usually gathered in a mixed stream that has a high level of contamination and varied properties. The quality of the recycled product can fluctuate and does not always meet the quality standards of typical virgin raw materials.
For upcycling to occur, a specific use for the recycled material must be identified at the product design stage – recycling would then happen accordingly. For example, most demolished concrete is currently recycled to produce crushed concrete. This contains coarse aggregate, fine cement, mortar particles, rubble, brick and other contaminants. This crushed concrete is used to replace rock when building roads and is considered a down-cycle because the recovered material replaces a material with lower commodity value.
Such a material stream – resulting from recycling and consisting of several mixed materials with a reasonably wide quality range – must undergo stringent filtering to qualify as a raw material in another production process. These activities, along with the need to keep higher safety margins, increase the cost of using recycled materials for manufacturing businesses.
Research shows that strong segregation of waste at the source of generation, data management and tracking along the value chain could help to overcome this barrier.
2) Maintaining constant supply
Keeping up with demand when recycled material or recovered content becomes a raw material in another supply chain is challenging. Matching the supply and demand needs of two supply chains requires careful inventory planning to avoid under- or oversupply. This drives up inventory holding costs. Designing production processes with the flexibility to switch to virgin raw material during supply disruptions results in asset under-utilisation and drives up working capital costs.
Once again, robust data management and cooperation with supply partners is key to overcoming this barrier.
3) Modifying the production process
If the properties of the new material are different to that of the virgin or traditional material, the manufacturing process itself might require modification to accommodate it. In the case of using recycled concrete, which contains residue cement mortar on the surface, producers need to be able to manage increased water absorption as a result.
New infrastructure will be needed to process the additional material stream if recovered material partially replaces traditional raw materials in this product. These changes are usually capital intensive and require investment. For example, new tools and methods will be needed to comprehensively model and evaluate supply and demand uncertainties linked to the use of recycled material. At the same time, getting accurate data on the quality and quantity of incoming streams will play a pivotal role in help to justify any investment in scaling up these processes.
4) Addressing demand uncertainty
Uncertainty of demand is another major issue for the industry. If manufacturers pass on the additional costs and risks of providing a greener product to the market, demand for that product may not be high enough to create a stable market.
This instability risk discourages producers from investing to scale up their operations to reach economies of scale. Creating a stable and consistent market pull for those products will provide producers using recycled materials with the necessary stability to operate, as well as to drive up productivity to compete.
5) Adapting incentive programs
Traditional manufacturing organisations use standardised processes to help them produce more efficiently while maintaining product quality. The introduction of new waste-derived, recovered or recycled alternative materials could disrupt these highly-standardised or optimised processes, however.
The key performance indicators (KPI) of production staff are usually tied to limiting production process variations. Incentivising staff to maintain the status quo in this way increases asset productivity and encourages them to meet production targets. However, this kind of approach is difficult to maintain when using recycled or recovered material due to the impact on production processes of the variations discussed in the previous points.
Unless traditional incentive schemes are changed to allow for these disruptions – perhaps even welcoming them as innovations or part of a wider green initiative – the traditional performance system will oppose this kind of change or transformation.
Finding the solutions
These barriers have a variety of solutions. While some require supply chain transformation, others need extensive collaboration and cooperation with value chain partners to reduce risks or redesign products for optimal integration.
Generating, managing and exchanging high-quality data is a universal solution. Developing stable demand for greener products is among the most prominent solutions to resolving most of the other barriers. Ultimately, we must acknowledge that establishing a circular economy will take decades and multiple iterative steps. Introducing waste-derived, recovered or recycled material to products is an early milestone in this long path towards a circular economy.
[box type=”note” align=”” class=”” width=””]License and Republishing
Written by